A Complex Lab Installation Project in the Bay Area
Our team recently completed a large, complex lab installation project that spanned four phases and required a high level of precision and creative problem-solving. The project involved the coordination and installation of 54 fume hoods, 130 agility tables with risers, 788 linear feet of lower cabinets, counters, and backsplashes, and more.
Project Overview
One of the challenges we faced was limitations with the on-site elevator, which presented a significant obstacle in terms of delivering lab equipment to the second floor safely. To overcome this, we used a Gradall to lift and transport the equipment while adhering to all safety protocols.
Despite the scale and complexity of the project, we were able to complete it on time and to a high degree of detail. Read on as we will delve into the details of this lab installation project and the problem-solving skills we used to get the job done.
No room for error:
Expert fume hood installation for this lab project.
The installation of 54 fume hoods required meticulous attention to detail. There was no margin for error as the fume hoods had to meet squarely with the ceiling and precisely match the building infrastructure, including electrical and ventilation systems.
This required close coordination with the general contractor and other trades, like electricians, to ensure that all this complex equipment fit together seamlessly with the building infrastructure.
Our team also installed monkey bars on the inside of the fume hoods to facilitate maintenance and repair, further emphasizing the importance of detail-oriented work in this project.
"The fume hood installation was definitely one of the most challenging aspects of this project.
We had to be very precise and careful when installing them from the floor to the ceiling. It was a time-consuming process because they had to be perfectly aligned with the ventilation conduits, and we couldn't afford to make any mistakes. Every piece had to be exactly right."
— Carlos Lopez, Master Lead Installer at All Modular
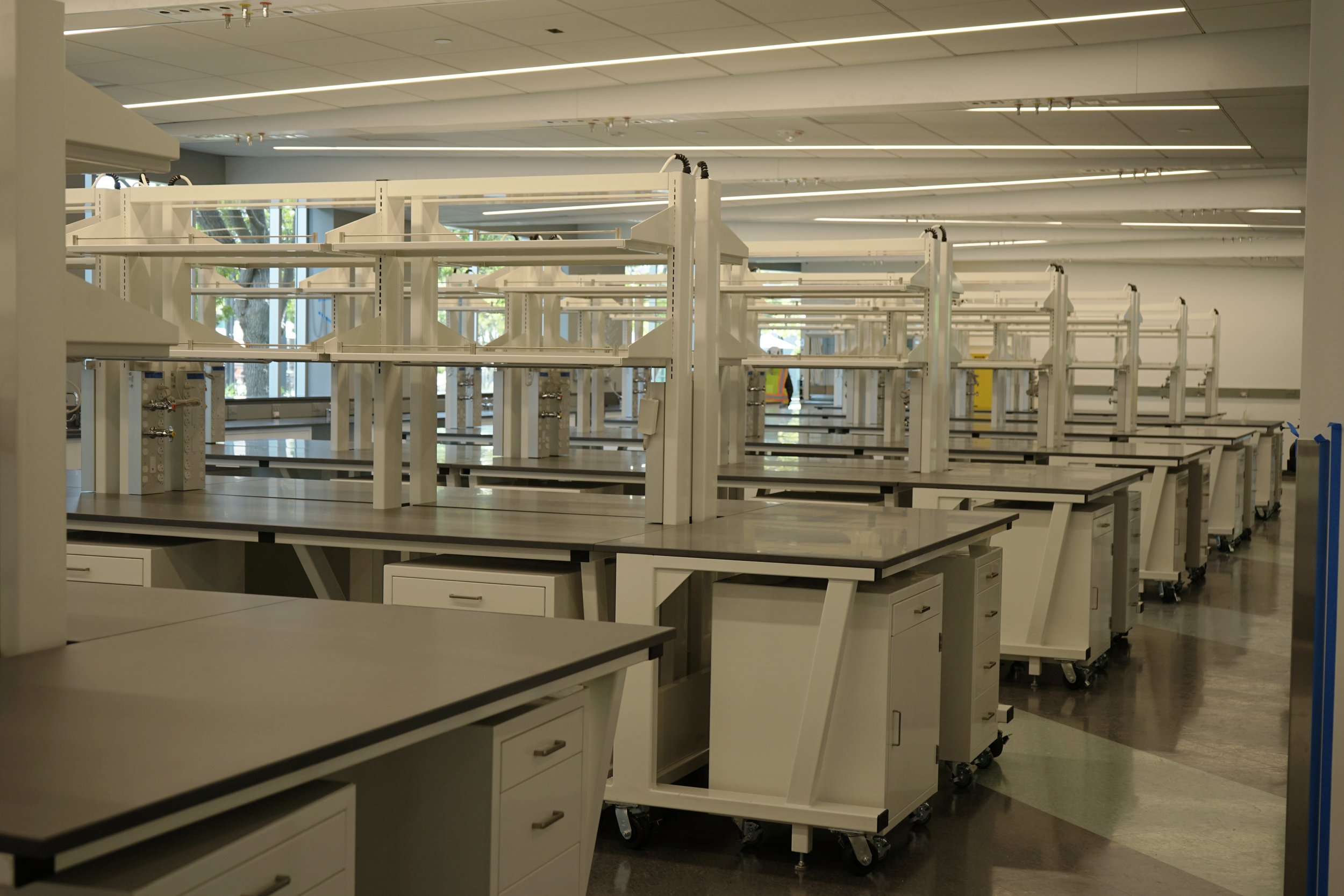
Expertly installing hundreds of lab tables and cabinets.
As part of this lab installation project our team delivered an expertly assembled 130 agility tables, complete with epoxy tops and shelving.
We also delivered 160 mobile cabinets and installed casters on each. Finally, we ensured that all items were placed according to the project's plan drawing.
While these units were designed to be mobile, we couldn't afford to make any mistakes due to the high volume of units and the need for them to seamlessly integrate with the building infrastructure, including power outlets located in service panels along the ceiling.
Every single unit required precise installation.